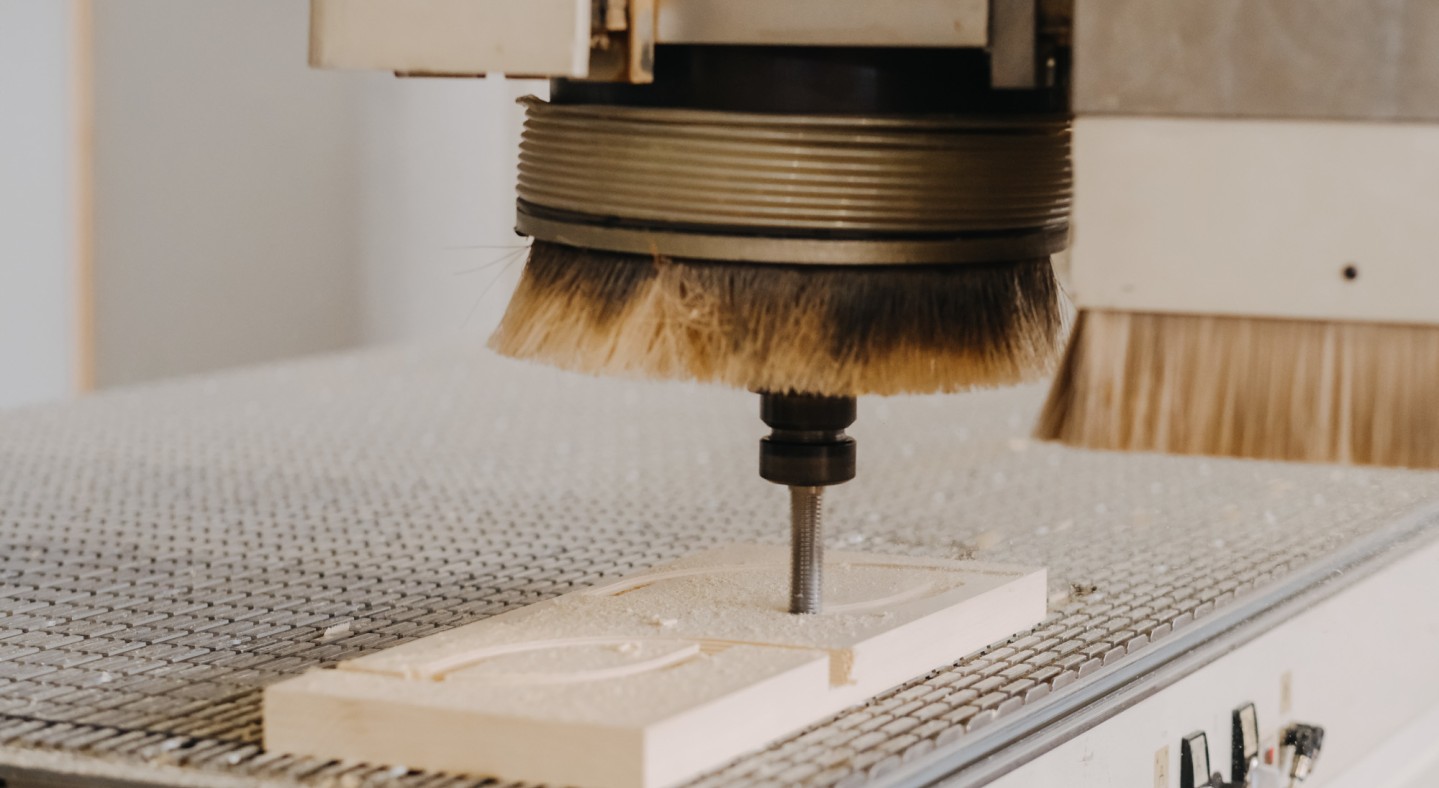
Efficiency Enhancement at Master Level
A furniture manufacturing company was faced with the fact that the productivity of some of its production machines showed a significant deviation from the reported 80%.
The result was drawn solely from machine cycle times, production data and engineering calculations collected on paper. When the operators were asked how this was possible, there was always an explanation, which was always based on reasons beyond their control (e.g. raw material not arriving on time, machine maintenance, tool breakage, power failure).
The company management was not satisfied with the credibility of the data. They wanted to find a solution that clearly explained the situation and did not give the opportunity to shift the blame.
Identifying the need
The company decided to implement a measurement system that would show the real times and actual data, without employee bias. They precisely defined which production data they needed from each machine in order to achieve the desired goal. To extract this data, they approached us as their development team to deliver a solution for both hardware and software.
Implementation
After mapping the exact requirements, it became clear that it was necessary to collect data directly from the machines (start-stop, cycle time). At the same time, the operator must be given the opportunity to react immediately in the event of downtime and to justify the downtime. Therefore, a solution was needed that would be connected to the machine control and at the same time would allow for employee interaction. In view of these facts, we decided on an operator panel equipped with industrial data acquisition units.
The data acquisition units were used to collect in real time and sort into a database the actual machine cycle start and cycle stop times. In the system, we provided a closed interface for the recording of products, orders, machine groups, machines, job indexes and their parameterization.

Real-time data
On the operator panels, the employees could see the following data for the given production machine in real time (on a second basis):
- Product name
- Ordered quantity
- Manufactured quantity
- Current cycle time
- Timing (deviation of the prescribed and machine cycle time in %)
Downtime reason handling
If the production machine stopped and the next piece did not arrive within the predefined time, a downtime reason window popped up, in which the operator had to select the actual reason for the downtime.
Remarkable result in production
With the OEEm industrial data collection system, the productivity of the machines was successfully increased from 30% to over 60-70%.
Change in employee attitude
There was a big change not only in production, but also in employee attitude. When the operator panels were installed but the data collectors were not yet connected, production efficiency suddenly jumped by more than 10%. So the simple placement of the operator panels (without technical function) had a psychological effect on the workers, which resulted in an immediate improvement in their performance.
I Want This Too!
Do not hesitate to contact us!
