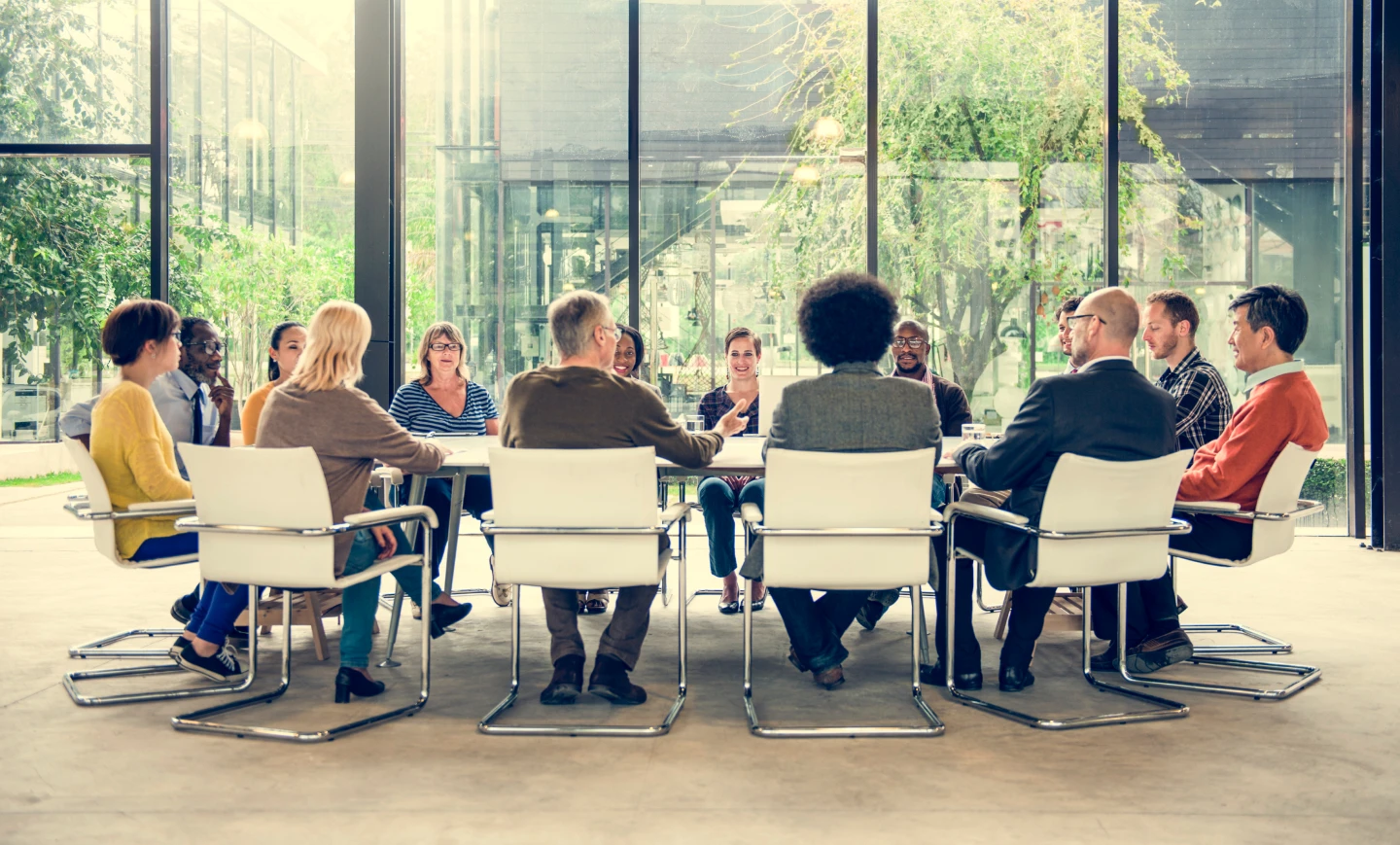
FAQ
Accurate answers to common questions.
Frequently Asked Questions
Find answers to the most frequently asked questions here!
The real-time recording of all parameters required to manufacture a product (such as raw material identification, manufacturing technology parameters and processes, quality indicators, employee identification, etc.) into a database.
There are many benefits to using the system, such as access to up-to-date data and the ability to intervene immediately in production based on this data, increased efficiency, energy savings, etc.
The OEEm industrial data collection system collects data generated during production processes, regardless of industry or production machine. It organizes this data event-oriented on the timeline based on intelligent logic. This event-oriented approach allows users to access real-time and event-based information about the manufacturing process.
The implementation process involves a technical survey, followed by a specific technical specification and quotation. While the equipment is being procured, the infrastructure conditions need to be established. The actual software implementation follows the installation of the equipment, in which the manufacturing processes are digitized using rule systems. The handover of the finished system is followed by a test period and training.
We recommend the OEEm system to all manufacturing companies that want to digitize and optimize their manufacturing processes, regardless of industry or production machine.
OEEm cloud is beneficial for those who value flexibility and easy implementation, as well as getting access to enterprise solutions with a smaller investment. OEEm cloud is generally recommended for environments with 5-10 production machines.
We recommend the OEEm on prem system for environments with many production machines where off-site data storage is not allowed and customized, supported implementation is important.
The payback period depends on the manufacturing process and the size of the plant. Based on our experience, this is around 6-18 months, but it is important to mention that our system primarily provides data to optimize processes, thereby reducing the payback period.
The implementation of the OEEm system strongly depends on the willingness of the client's employees to implement it. The specific time typically ranges from 3 to 12 months, but we will give a more accurate estimate of the expected time after the technical survey.
The OEEm system makes it easy for employees to access the information they need, which reduces their administrative burden. Simplifying administrative tasks prior to system implementation can free up additional resources.
The OEEm system objectively records live (real-time) data generated during production into the database as it progresses along the timeline, eliminating the possibility of human error and subsequent manipulation. The data collected in this way can be reliably used to create any report or action plan.
Of course, multiple locations can be connected with either version. In the case of the OEEm on prem system, the locations can be connected using an IT network (e.g. VPN). The data can then be collected in a central database, which can then be logically grouped at the location level. In the case of OEEm cloud, connecting locations is not a problem, as the center is located in the Digitop cloud.
Do you have more questions?
Do not hesitate to contact us!
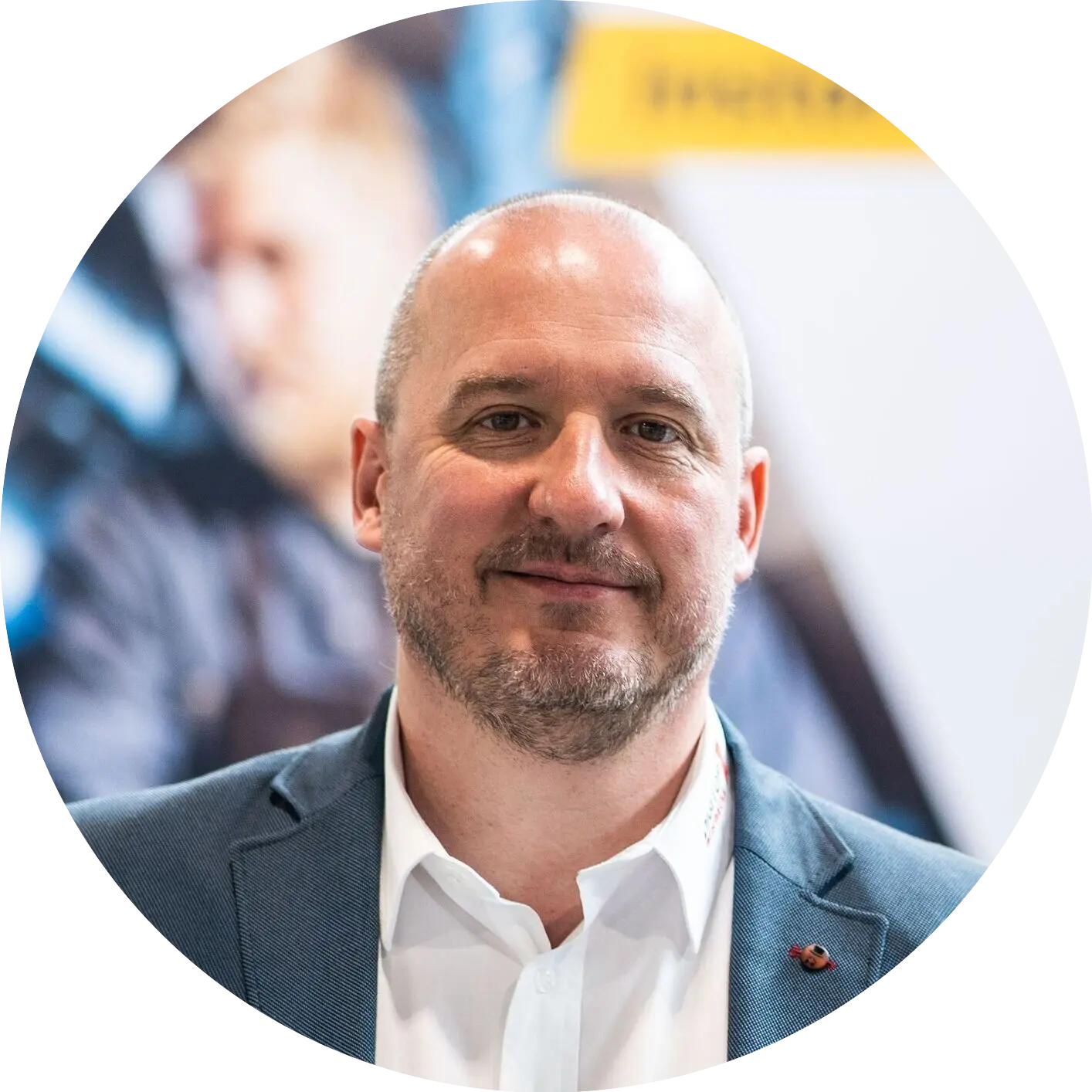