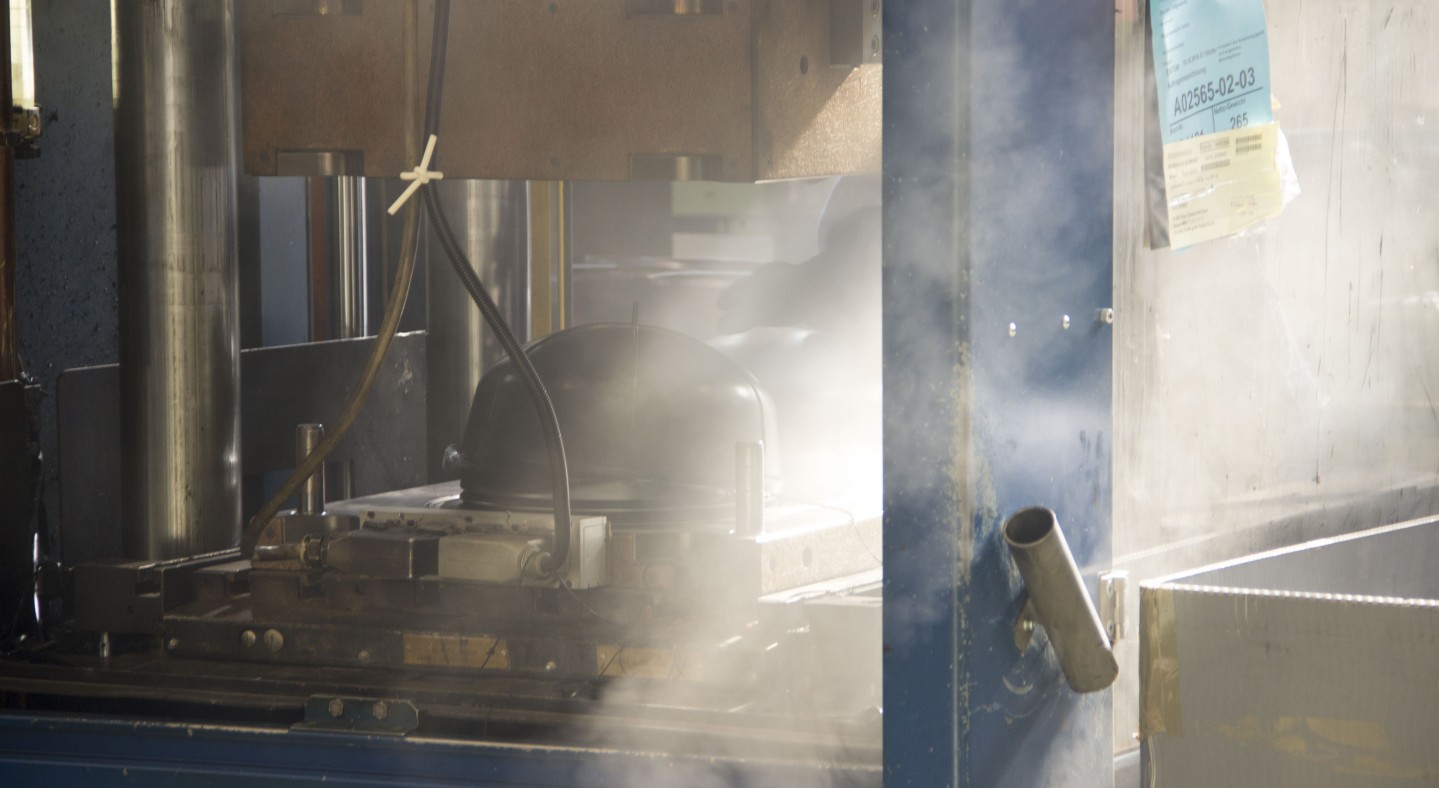
Display and Timing
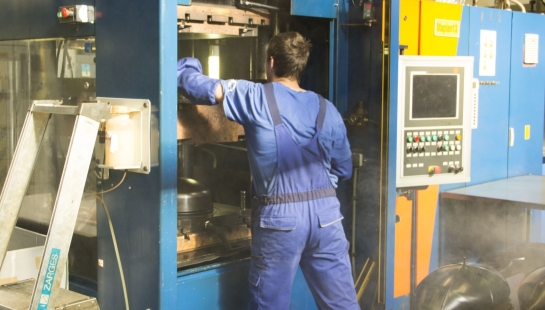
Problem
A tire manufacturing company had difficulty operating their machines efficiently due to layout problems. Each operator had to supervise 6 machines in parallel, which were located on two different lines. Due to the long baking times, the workers had to constantly move between the machines and could not see overall where the machines were in production at any given time. They also needed to reduce tool opening times to increase energy efficiency.
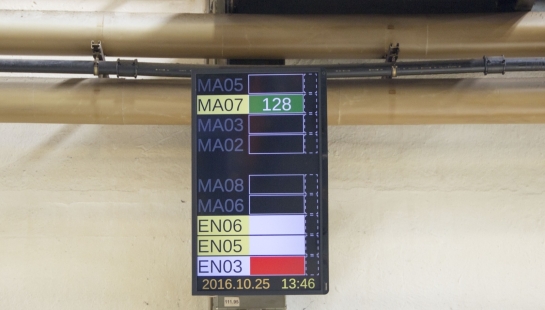
Solution
The company installed data collectors on all of their machines, which send information about the production cycles to a central data processor. A wall display was also installed at the end of the production lines, which simultaneously showed the countdown for the 6 machines. A light was installed on each machine, which allowed the operators to easily monitor the operation of the machines and the baking processes without having to go directly to the machine.
Result
With the introduction of the system, the tools were opened much less, so more cycles could be produced on the machine, and less energy had to be used due to the reduced tool opening time. The workers knew exactly what to do when, so efficiency increased. Overall, this solution not only increased the performance of the machines by introducing the correct timing, but also resulted in significant energy savings by avoiding unnecessary tool heating.
I Want This Too!
Do not hesitate to contact us!
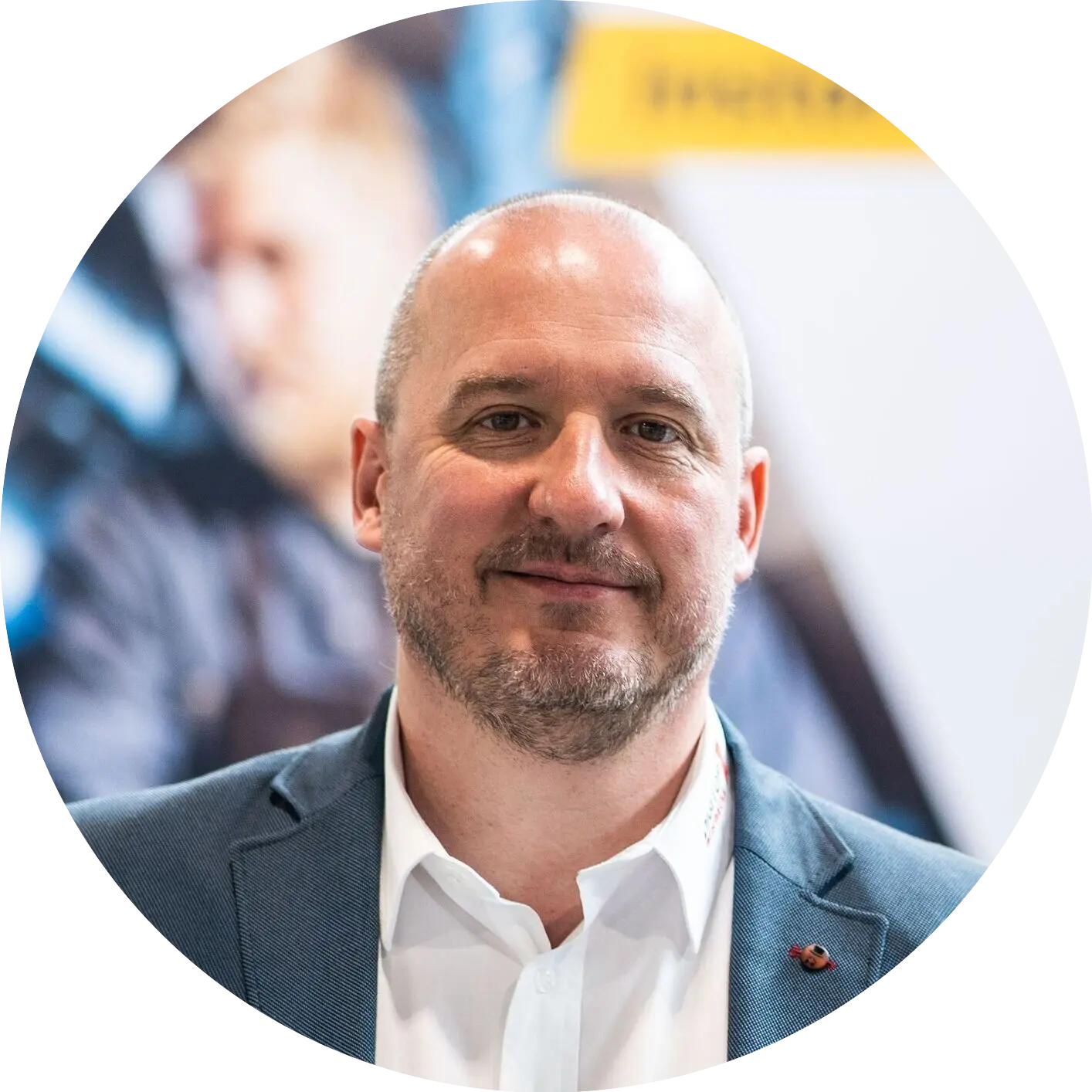