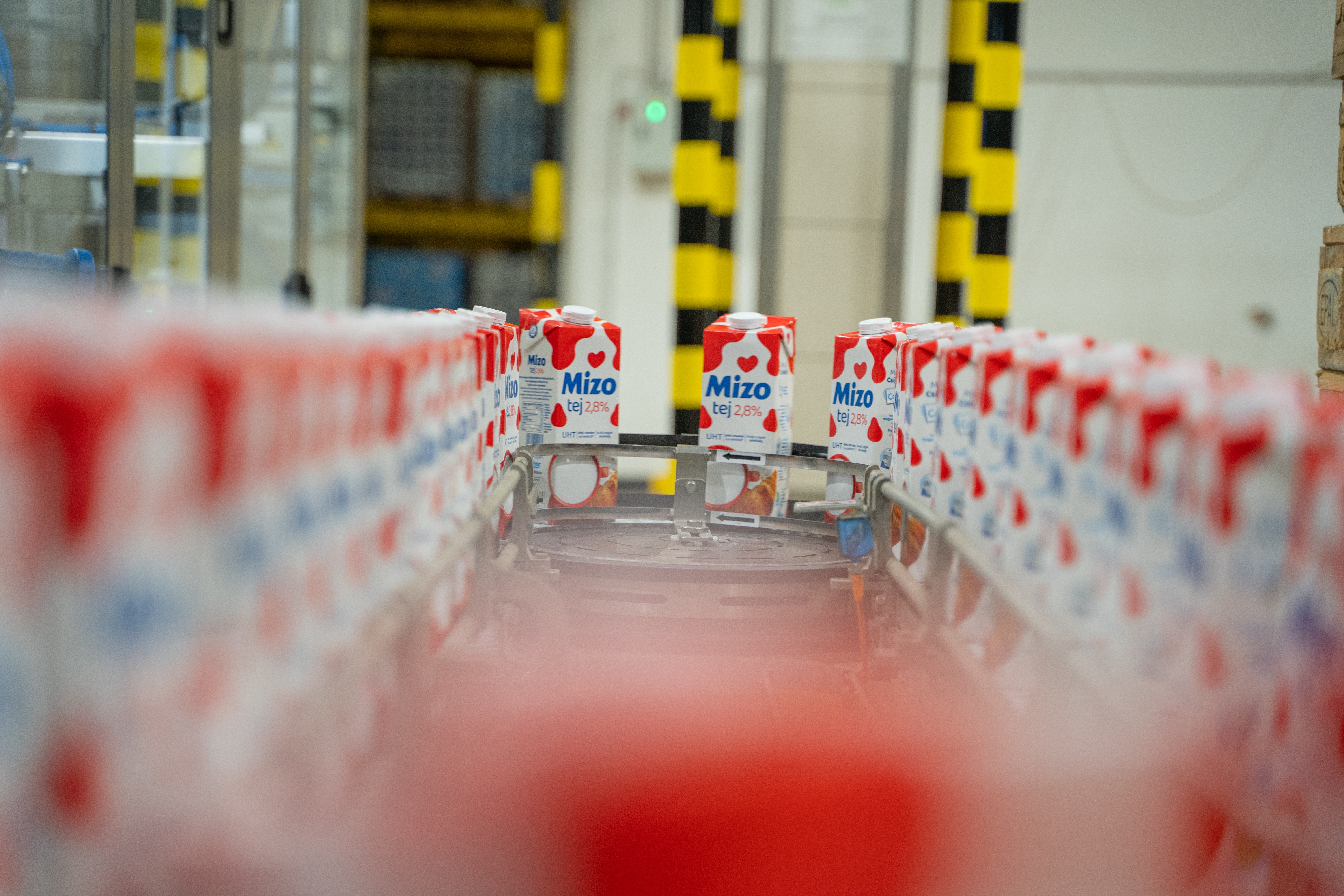
Production Digitalization in an Entire Group of Companies - in Just 10 Months
In 2023, the Bonafarm Group approached us with the following production digitalization needs.
Problems to be solved
- Replacing the slow, paper-based data collection, thus speeding up the flow of information,
- eliminating the huge amount of manual administration and thus the countless possibilities for errors,
- Replacing inaccurate information from production with accurate, real-time data.
Neque porro quisquam est qui dolorem ipsum quia dolor sit amet
Vivamus eget facilisis nulla. Cras fringilla dolor at magna aliquam, consectetur auctor purus porta. Etiam porta, lacus vitae ultrices sagittis, ipsum arcu laoreet erat, eget aliquam tortor quam eget metus. Integer efficitur vulputate vehicula. Etiam tincidunt nec lorem vel posuere.
The plan was to introduce a digitalized system, replacing paper-based data collection and replacing manual processing with an automated, machine-based solution.
It was essential that the new system be integrated with the existing enterprise resource planning system and that the efficiency of the production lines could be measured in real time.
What was needed to make this happen?
The first and most important step was to define their exact needs and to set up a project team who prepared the documentation based on the needs.
This was followed by the tender announcement and the selection of the winning external team.
This is how they chose the Digitop OEEm system.
After the selection, before starting the work, we had to answer the following questions:
• What exactly do they produce?
• Under what conditions?
• What does the manufacturing process look like?
• What are the pitfalls, the obstacles?
• What are the special expectations?
A key factor of the project was that the construction in the food industry requires special attention to hygiene aspects.
How did we implement it?
5 different food sectors were involved: dairy, meat, wine, slaughterhouse, poultry processing. In total, we installed approximately 200 measuring points at 10 locations, trained 500 employees on how to use the system, and we had only 6 months from the tender to the live launch.
The existing OEEm software system had to be customized to the Bonafarm Group based on the requests, which meant that we equipped the basic system with many additional functions.
During the on-site installations, it was necessary to build a local network, which involved the installation and commissioning of data collection cabinets. It was also necessary to install the counting sensors in the production, as well as the already mentioned operator panels and displays, on which the production can be monitored.
During the physical installation, we had to take into account several conditions, such as food industry regulations, material use and protection against cleaning (washing).
Installation in numbers:
Due to the physical distance of the sites, we drove almost 20,000 kilometers in Hungary, used 55 kilometers of cables and 4.5 tons of stainless steel for the connections.
Even after the live launch, we monitor the operation of the system on a weekly basis and continuously consult with the project team.
The OEEm system installed at the Bonafarm Group is a great example of how we deliver the most modern production digitalization solution flexibly, tailor-made, on time.
I Want This Too!
Do not hesitate to contact us!
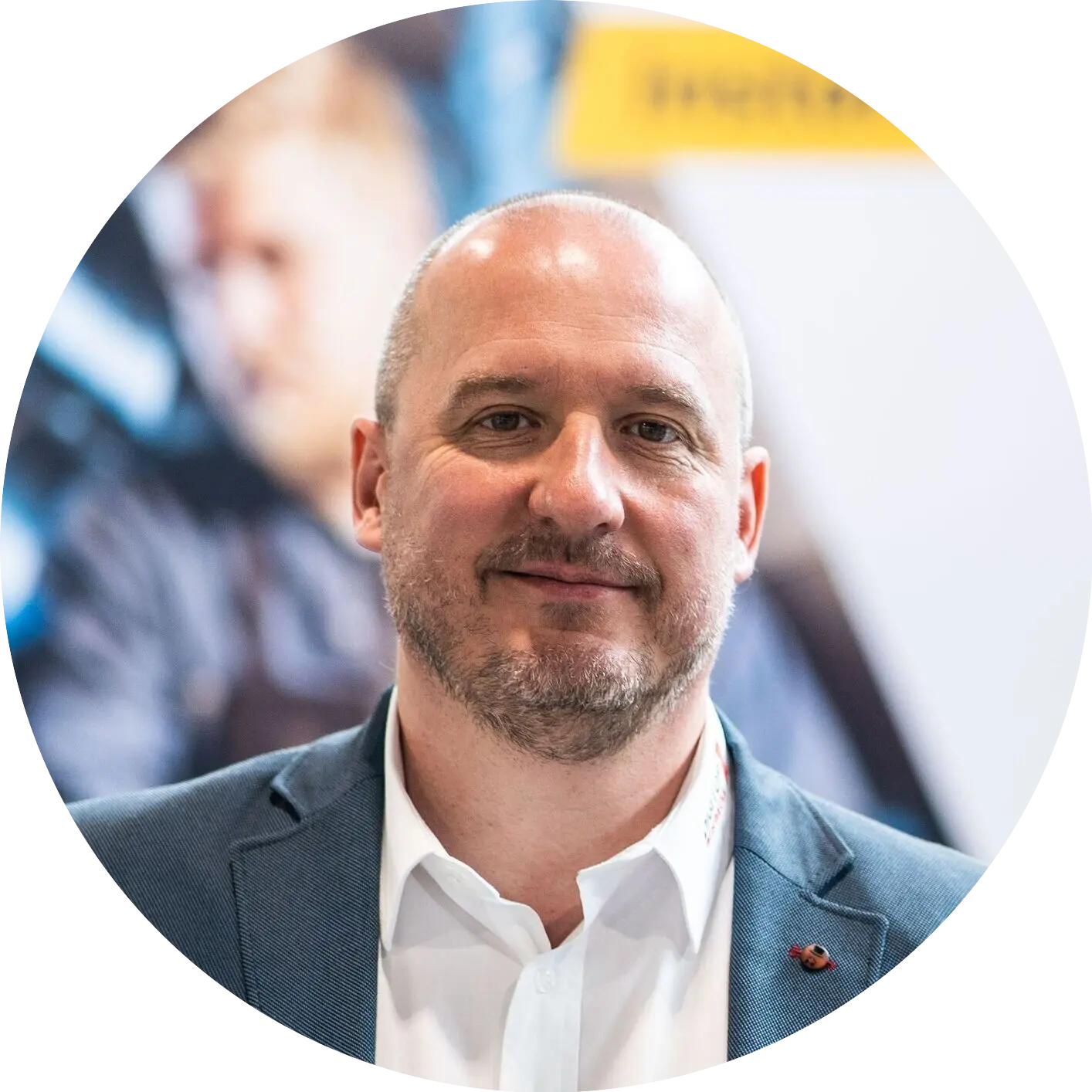