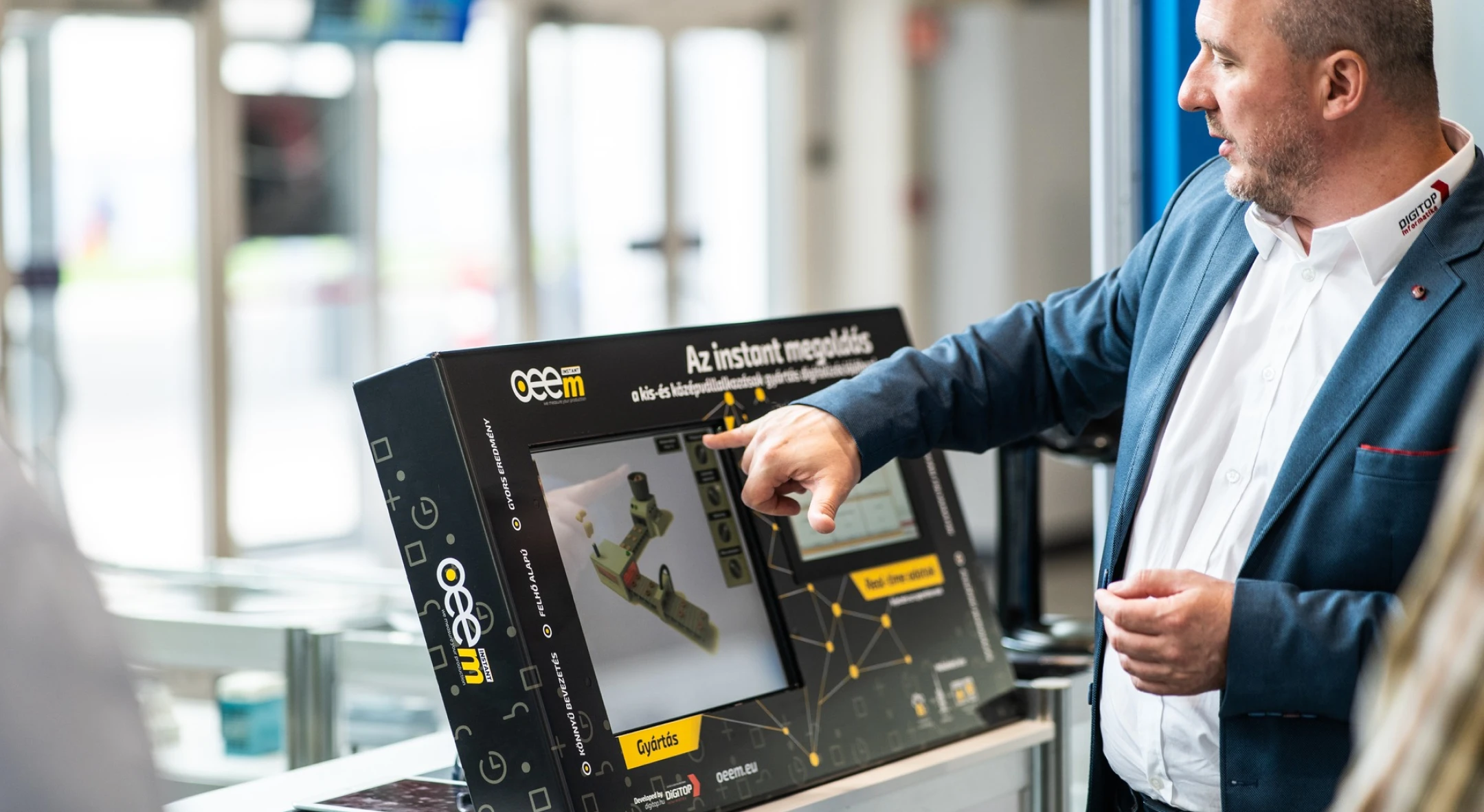
Our solutions
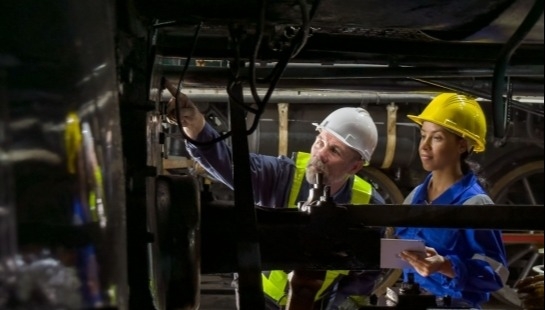
Optimize Your Production Process
The OEEm manufacturing monitoring system tracks production processes in real time and quasi-digitalizes the entire manufacturing process. However, in order to optimize production, it is not enough to simply collect data; it is also necessary to analyze it and intervene in the production processes based on the conclusions drawn from the analysis. The OEEm reporting system provides the facts and figures for this.
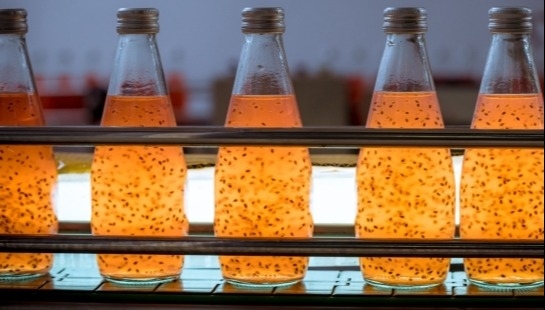
Tailored for Series Production Companies
The optimal target area for optimal use of the OEEm system is a company that produces in series production, since when products are produced in series, there is the possibility of direct monitoring and digitalization of automated processes.
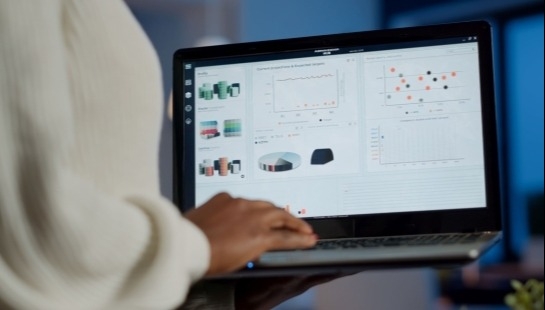
Saving and Profit Increase
The analysis of the data and reports generated by the OEEm system highlights the areas that cause losses, thus avoiding unnecessary investments. In this way, savings can be achieved and profits can be increased.
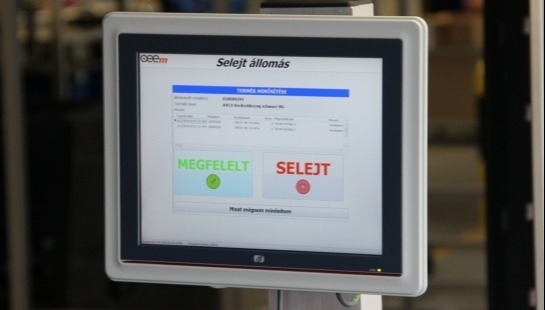
Supports Quality Assurance
Scrap analysis and production digitalization are fundamental tools for quality assurance. With scrap reason analysis, we can improve the quality of production, and the collection of technological parameters during production provides all the data for quality assurance.
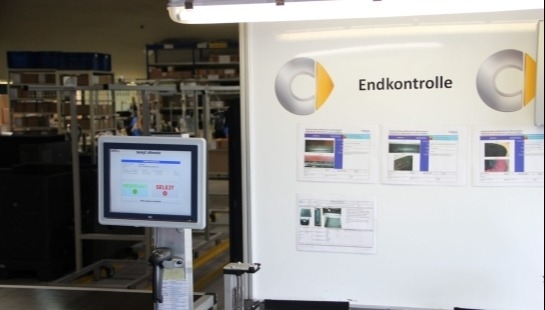
Scrap Analysis
The scrap analysis module makes the quality control of manufactured products faster and easier, all with minimal administrative burden. The analysis of scrap reasons gives the opportunity to intervene indirectly in the production processes.
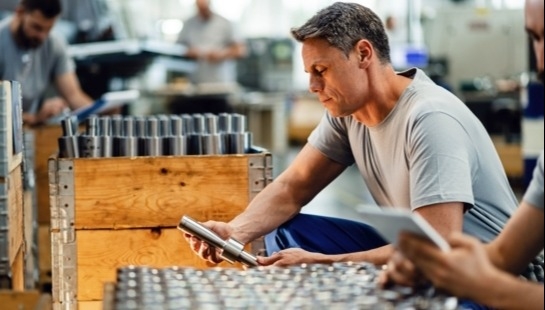
Product Identification
Whether it is individual, container or batch identification, OEEm is the right choice to ensure that the product can be tracked throughout the entire manufacturing process. With product identification, it can be precisely determined from which raw material, with which production parameters and with which quality indicator the given product was manufactured.
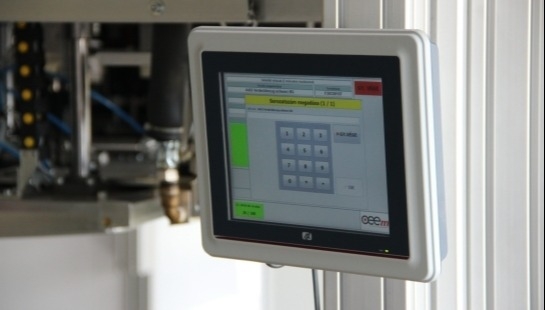
Downtime Analysis
One of the important parameters of the OEE indicator is the analysis of downtimes. For this, the OEEm system allows downtime reason definition with minimal administration and free of human error.
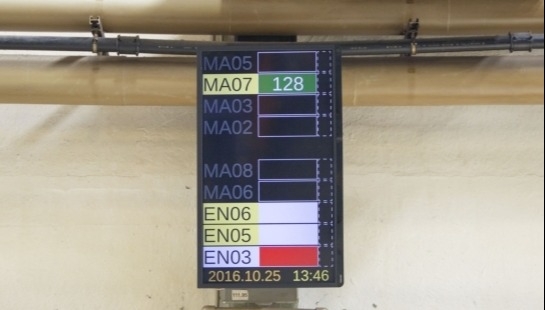
Production tracking monitoring
Tracking the product from raw material to finished product. During the process, we record in a database who produced the product, from what raw material, through what production processes, with what technological parameters, at what rate and in what quality. In the case of production tracking, we do not intervene in the processes.
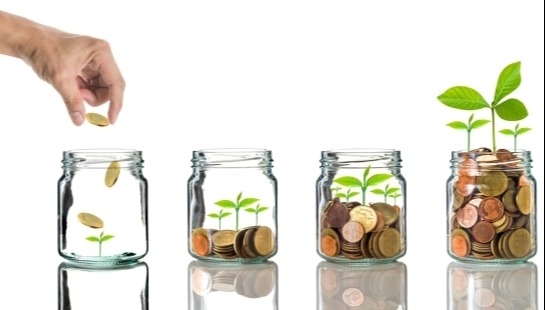
MES system
Manufacturing Execution System (MES) - Our integrated software system provides real-time data on plant activity from sensors and manufacturing processes. It uses the data to manage manufacturing processes by tracking, documenting and controlling every step of production, optimising its outcome. This solution not only monitors but also controls production.
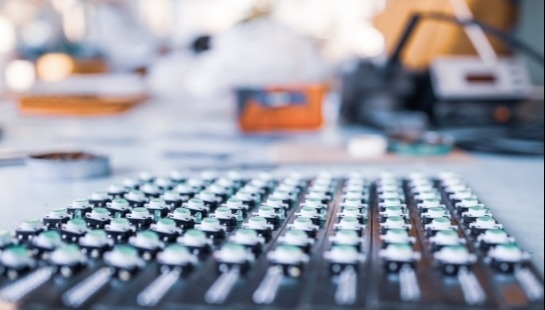
Sequential production management
Sequential manufacturing provides a sequential ordering of manufacturing processes based on a predefined sequence. In manufacturing, products are always produced and packaged according to the sequence, thus avoiding, for example, the packaging and delivery of non-conforming finished products in non-sequential packaging.
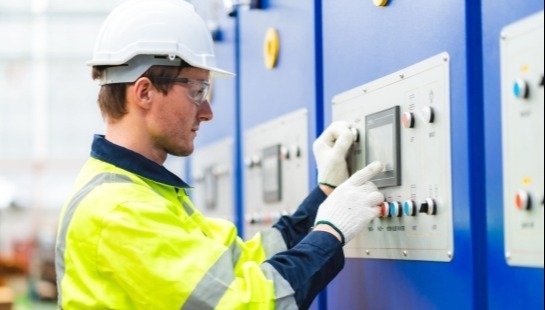
Energy management
Energy management can be used to ensure that the site does not exceed its predetermined maximum energy demand during production processes, thus avoiding the negative consequences of overconsumption.
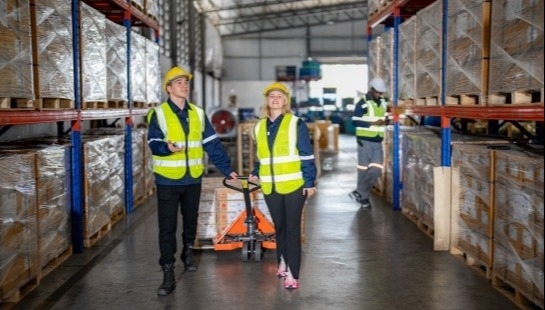
Inter-production logistics
Full logistical status tracking: i.e. from the receipt of raw materials to the delivery of the finished product, it is possible to track where a given product in production is in the manufacturing process, from a warehousing perspective and based on its status in the manufacturing process. This gives a transparent picture of the status of a product on a given pallet.
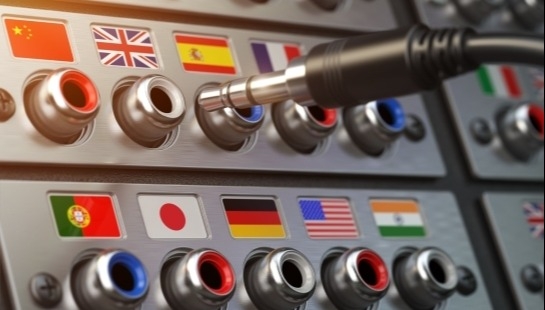
Multilingual interface
The built-in translator module allows you to translate the interface into any language, in addition to the available multilingual layouts.